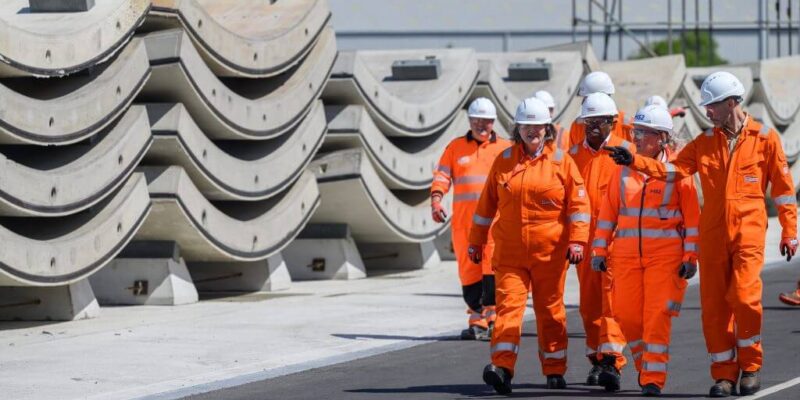
The production of over 83,000 concrete tunnel segments for High-Speed 2’s London tunnels has started at Strabag‘s new facility at Hartlepool’s docks in County Durham this week.
A portion of the tunnel segments will be utilized to build 8km of twin bored tunnel for the High Speed 2 (HS2) Euston tunnel between Old Oak Common and Euston station. Also, concrete segments will be employed for 5.5km of twin bored tunnel for the Northolt tunnel east project.
As reported, the move signals a step forward following HS2 Ltd.’s confirmation in April that work on the Euston tunnel, organized to start in 2024, had been halted.
The concrete segments will be a pivotal part of tunnel rings – each with an 8.8m outside diameter, estimated 350mm thick and weighing 7t. Totally, 96 concrete segment rings will be manufactured daily at the site, with teams of 30 working in shifts across 24 hours, seven days per week.
Strabag was granted the contract to produce the segments in October 2021 and launched its production site in a unit at Hartlepool’s docks formerly used for the oil rigs fabrication.
The new facility has a mechanical segment carousel and reinforcement hall, where telemetry-controlled robots will create the reinforcement cages needed for each segment, promoting shorter turnaround times and constant output quality. HS2 Ltd. conveyed that the automated production of steel reinforcement cages would also decrease wastage and enhance efficiencies in comparison to non-automated techniques.
Additionally, Strabag has reinstated the rail head at the docks and the related rail connections bordering the site to decrease truck movements. Also, it is employing the local supply chain, sourcing aggregate from local quarries, and utilizing UK recycled steel. The segments will be moved by rail to HS2’s London logistics hub, part of HS2’s commitment to lower carbon emissions in construction.
It starts in the summer, and a 20-carriage train will leave the site each day over six days, rising to two per day as production boosts.
The segments will be transported from the logistics hub and by an electric multi-service vehicle (MSV) to the neighboring construction sites and moved onto the four giant TBMs that will be building these tunnels.
Andy Dixon, Strabag UK managing director, claimed: “This is an extremely exciting day for Strabag’s UK operations. Our new factory in Hartlepool allows us to manufacture products for HS2 in the North East of England by giving new life to a vacant site and bringing over 100 new skilled jobs to the area. The increased use of automation enhances production efficiency, creates a safer environment for our staff as well as creating new technology related job opportunities.
“In addition, having direct access to the rail network means that we can take a significant number of lorries off of UK roads. This creates a more sustainable solution in the way that we transport tunnel segment rings to the tunnel boring machines building the London tunnels for HS2, resulting in a reduction in our carbon footprint.”
HS2’s primary works civils contractor Skanska Costain Strabag joint venture (SCS JV) is building HS2’s London tunnels. James Richardson, SCS JV managing director, declared: “The tunnel segments manufactured here in Hartlepool will be transported by rail to our tunnel boring machines, forming the high-speed tunnels in the heart of London.
“By using rail instead of road to move over 83,000 segments, we avoid over 56,000 lorry journeys and reduce CO2 emissions by 76%. At all stages of the manufacturing, transportation and installation of these tunnel segments, we will ensure the building of a cleaner, greener railway and unlocking the social benefits HS2 can bring across the UK.”
In addition, Ruth Todd, HS2 Ltd. chief commercial officer, pointed out: “Over 3,000 UK based businesses are already working on the project, with over 28,500 jobs directly supported, with many more through the supply chain. As more phases of the HS2 program begin, there will be many more opportunities for businesses across the UK to get involved in this once-in-a-generation megaproject.”
While the Hartlepool facility will be employed to make the tunnel segments for about three years, the investment from Strabag in the site is envisioned to support a longer-term UK investment strategy.