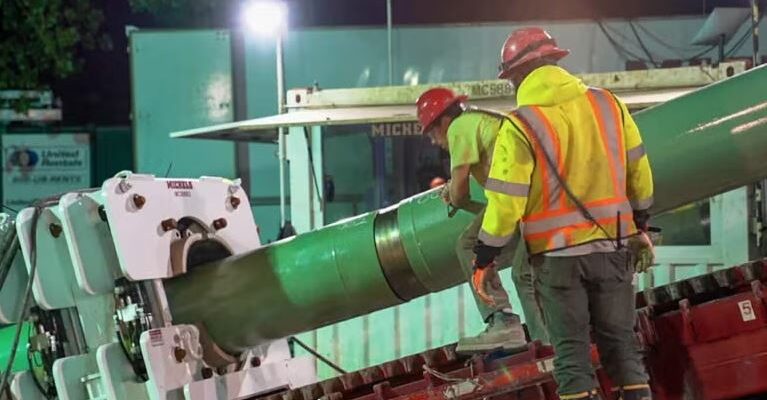
In order to installing an electricity transmission line under the East River in New York, Horizontal directional drilling (HDD) has been used.
As a buried transmission line to deliver hydroelectric power from Canada to the New York metropolitan area, the Champlain Hudson Power Express (CHPE) is 545km-long and starts at the US-Canada border, travels south through Lake Champlain, beneath the Hudson River and crosses the East River to end at a new converter station in Astoria, Queens.
Linking Randall’s Island and the Astoria converter station, the HDD pipeline is due to house fusible PVC carrier pipe for the project’s fibre optic cables and installed in two parallel 1,585m drives under the East River. Kiewit is the contractor on the project and Michels Trenchless the subcontractor for this trenchless segment.
Considering the depth of the East River,HDD was chosen and the project was originally designed to have a pipe string out on Randall’s Island, whereas space constraints, including rail crossings, highway overpasses, and a sports complex and recreational facilities in the area, meant pipe string out was not feasible, and an approach with a smaller footprint was needed.
With the aim of providing a weld-free solution that allows for the casing pipe to be cartridge-fed from the launch rig side, eliminating the need for string out on the exit side, Northwest Pipe Company supplied 3,170m of 508mm steel casing pipe with Permalok HDD joints for the crossing.
The Northwest Pipe’s Permalok plant in Missouri was the location of manufacturing 345 sections of pipe in 9m sections.
Two pilot bores, commencing at 309mm diameter and upsizing to 864mm, were drilled by Michels to prepare for the HDD pipe installation. The bores extend from the onshore launch rig at the Astoria converter station, 45m below the East River, to an exit rig on Randall’s Island. Being designed to absorb the vibration created by the spinning pull head, the first Permalok HDD joint was welded to a 36.5m section of uncoated steel casing, while the pull head is used to guide the HDD pipe along the pilot bore path as it advances. In order to pushing the pipe into the pilot bore and the interlocking design means no field welding is required, the drill rig also uses a hydraulic press.
According to Michels assistant operations manager Jeremiah Yliniemi: “It was a simple process for a complex project.The Permalok HDD joint is very easy to work with and installs much faster and more efficiently than welding traditional HDD pipe strings.The biggest cost savings are on welding crews and other equipment needed for pipe string layout and pullback assistance, plus it can all be done on the space you are already using.”
The time duration of completing the installation was a tight timeframe. While completion of the first 1,585m drive was done in less than 2.5 days, its average rate was of 30.5m per hour, and the second drive even more quickly.