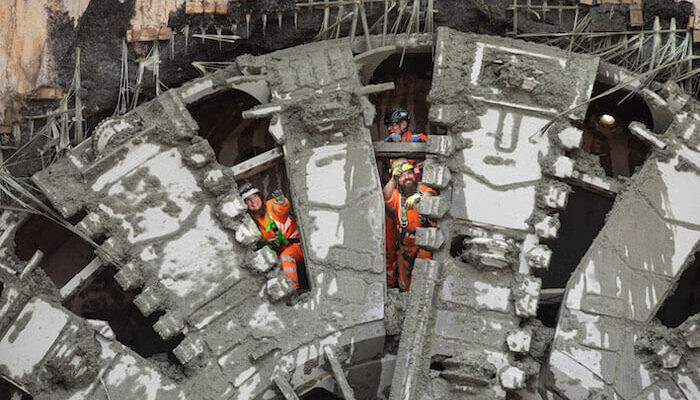
Digging the longest tunnel on the rail project, HS2’s first TBM, which was commissioned around three years ago, has broken through at the end of her 16km journey beneath the Chilterns.
Being launched in May 2021, TBM Florence with 2,000-tonne weight is one of 10 machines excavating the 51.5km of tunnels on the new railway connecting London Euston with Birmingham, while its average advance per day is 16m and lined the tunnel with 56,000 pre-cast concrete segments.
In order to creating the twin-bore Chiltern tunnel, which runs from the South Portal near the M25 to South Heath in Buckinghamshire, two identical Herrenknecht TBMs were used. The determined date for tunneling by TBM Cecilia is the coming weeks.
While commissioning location of Florence and Celia were the South Portal, they are operated by HS2’s main works contractor, Align, a joint venture of Bouygues Travaux Publics, Sir Robert McAlpine, and VolkerFitzpatrick.
Each TBM is operated by a crew of around 17 people, working in shifts to keep the machines running 24/7. They are supported by over 100 people on the surface, managing the logistics and maintaining the progress of the tunneling operation.
In total, more than 450 people have worked on the tunnels and in support teams on the surface over the past three years. This includes a team that produced 112,000 precision-engineered, fibre-reinforced concrete tunnel wall segments at a temporary factory at the South Portal who completed their work just before Christmas, and a team processing the spoil from the tunnels.
Advancement of the London approach tunnels is undergoing by using four similar TBMs, whereas progress on Birmingham’s Bromford tunnel will be up to another two TBMs. Following starting up the two TBMs that supplied for the Euston Tunnel in current year, they stored under Old Oak Common Station until the government gives approval for the line to be extended to Euston Station in central London.
According to Align project director Daniel Altier: “The typical drive for a TBM was 5-6km and so the challenges in completing a 16km drive should not be underestimated. Florence and her sister TBM Cecilia were designed in partnership with Herrenknecht. They incorporate a number of innovations and technologies that have been introduced on TBMs in the UK for the first time, to enhance performance and safety. This includes ‘semi-continuous boring’, allowing our TBMs to build the rings that line the tunnels without pausing.”
He also added: “The mining of the tunnel is a fantastic achievement for not only the Align tunnelling team but also the earthworks team who have managed chalk excavated from the tunnels and placed on site, along with many other supporting functions. I would also like to acknowledge our supply chain partners, including TGT that provided the teams to operate the TBMs and MS with whom we designed and operated the slurry treatment plant; with 24 filter presses it is the largest in the world.”
HS2 Ltd executive chairman Sir Jon Thompson said: “There was still a lot of work to do but historic moments like today really underline the huge amount of progress that’s been made and the fantastic engineering skills we have on the project.”
The 80m beneath the Chilterns is this tunnel’s deepest point, and it passes under the M25, railway lines and twice under the River Misbourne. Extensive water quality, groundwater level and surface water flow monitoring was put in place prior to the start of construction, and HS2 said there had been no significant change to water quality during the tunnelling work.
The quantity of chalk and other material that was removed during the tunneling process is 3 million m3 and it is being used to create a grassland restoration project at the south portal, which is due to include 127ha of new landscaping, wildlife habitat and chalk grassland.
As the longest railway bridge in the UK, Align is also delivering the record-breaking Colne Valley Viaduct which’s construction of the deck now more than two-thirds complete.