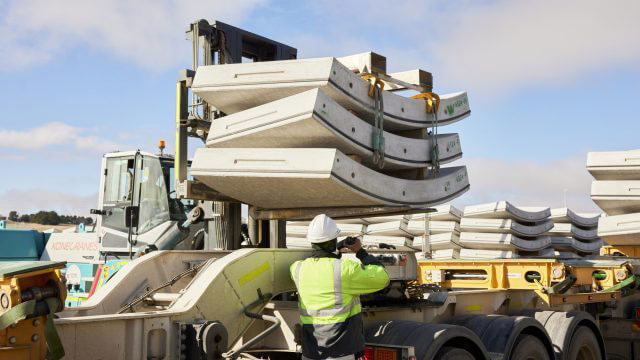
In order to providing the required 130,000 concrete segments for the 27km of tunnels for the pumped-hydro project, the Snowy 2.0 Cooma precast manufacturing facility has produced 100,000 of this quantity.
Being installed by the three TBMs used on the Australian project, more than 230,000m3 (over 550,000 tonnes) of concrete have been used to manufacture the seven-tonne precast segments.
According to Snowy Hydro CEO Dennis Barnes: “It was pleasing for the project to be manufacturing and investing locally, while also providing employment opportunities. About 200 people from the 3,000-strong Snowy 2.0 workforce work at the precast factory operated by our project contractor Future Generation Joint Venture.The facility supports local employment and also on-the-job training for a number of school-based apprentices from Monaro High.”
The process of checking the quality of every segment produced is undergoing by the precast facility that includes a concrete batching plant and onsite laboratory, whereas many of the raw materials, such as aggregates, are sourced from local quarries at Mt Mary and Nimmitabel.
Decreasing the production’s environmental footprint while improving the segments’ durability and performance, is the advantage of design of the concrete mix, which includes waste material.
Additionally, in order to automating the process of demoulding, cleaning and application of the release agent on the segment moulds carousels using robotics have been applied in the manufacturing process.
One of the two carousels has now been modified to produce the precast segments for the Snowy 2.0 inclined pressure shaft (IPS). The very steep 1.65km shaft will be excavated by TBM Kirsten and will link the underground power station with the headrace tunnel coming from Tantangara.
As the world-first force-activated coupling system (FACS), the IPS segments adesigned to withstand the powerful internal forces of water moving through the 10m diameter inclined tunnel.
Considering that installation of segments with FACS eliminates the need for a second tunnel lining, this improves the quality, safety and the rate of tunnel completion.
The number of IPS segments that is due to be produced by Snowy 2.0 precast factory is around 9,000, while nine used in each tunnel-lining ring. The first ring prototype has been completed, with mass production expected to start next month.
In January, Snowy Hydro announced the breakthrough of the final three metres of the power station’s 223m-long transformer hall cavern crown.
Almost 800m beneath the ground at Lobs Hole in the Snowy Mountains is the location of Snowy 2.0 power station, which following its completion the machine hall will be 251m long and 52m high and the transformer hall 223m long and 46m high. Together they will form one of the largest and deepest caverns in the world, big enough to accommodate the Sydney Opera House.