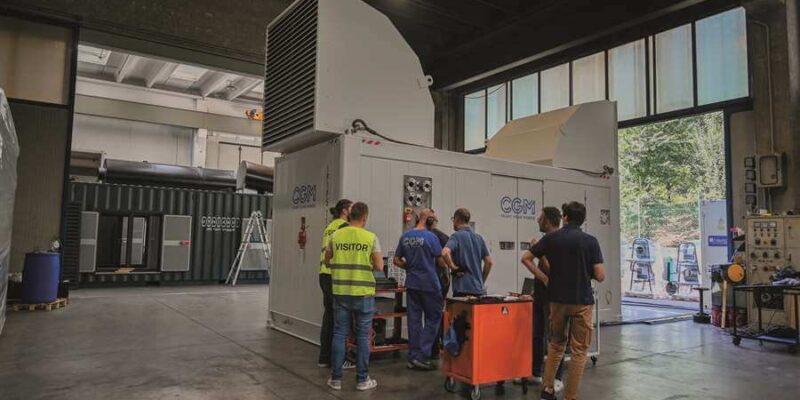
CGM, the generator set manufacturer, which has its headquarters in Vicenza, Italy, is supplying power for the construction site of the Fehmarnbelt tunnel. The project includes road and rail connections driving 18 km between Denmark and Germany and sets to deliver the world’s longest immersed tunnel.
The Fehmarnbelt project’s website reported that the journey between Rødbyhavn, Denmark, and Puttgarden, Germany, will take seven minutes by train and 10 minutes by car upon completion in mid-2029. Road users and train passengers will save almost one hour each way over the current ferry crossing.
The Fehmarnbelt link will remain open 24 hours a day, unaffected by ferry plans and weather. In addition, the connection will assist with reducing CO2 emissions by enabling traffic to use the shortest and fastest route while opening capacity on roads and railways.
Stefano Chilese, CGM’s Managing Director, described that his company has provided 20 gen-sets for the spreader pontoons used to specifically distribute sediment for land reclamation and for the protection layer pontoon, which is employed to install sheet metal on the seabed.
Chilese pointed out: “The 20 gen-sets feature 100-kVA FPT Industrial engines certified for EU Stage 5 emissions regulations; Mecc Alte alternators with special coatings; 12 IG1000 and Intellivision 5.2 controllers by ComAp; ABB’s electrical cabinets; and 18-in. touch control panels.” Housed in four 40-ft. High Cube containers, the units provide a total of 2 MVA (1.6 MW).
Additionally, CGM is delivering eight gen-sets housed in two 20-ft. DNV-certified containers for the two immersion layer pontoons were employed to position the tunnel sections underwater.
He also stated: “These eight gen-sets deliver 660 kVA each, in parallel. That is a total of 2,640-kVA prime power per submerged pontoon and 5.3 MVA – in total (4.2 MW),”
“These units are powered with Volvo engines certified for IMO Tier 3, using Stamford alternators with special coatings and type IG1000 controllers by ComAp.”
CGM gen-sets will deliver 7.3-MVA (5.8 MW) continuous power to this gigantic construction project in total.
Femern A/S, a state-owned Danish firm that will also be responsible for operating the tunnel upon completion, is leading the Fehmarnbelt construction project. The projected costs are envisioned to be approximately €7.4 billion, being co-funded by the European Union.
Tunnel entrances are positioned near Rødbyhavn and Puttgarden, which will be linked through new and upgraded road and rail links. For instance, the Danish railway from Ringsted to Rødbyhavn will undergo a substantial upgrade, containing two new electrified tracks, claimed to have a top speed of 200 km/h.
The immersed tunnel will be constructed utilizing 79 standard and 10 special elements. These will be manufactured onsite at a casting factory spread across six production halls. The building will make a standard element almost every two weeks for nearly three and a half years.
The total production time for each element will take nine weeks. The casting process takes place in climate-controlled halls to secure uniformity and quality, a requirement to acquire the 120-year operational lifetime of the tunnel.
Each ‘standard element’ weighs 73,500 tons and is 217 meters long. They comprise five openings, with two tubes for the motorway, two for the railway, and one service passage. Each ‘special element’ will contain a “basement” area to house associated technology; this will ease the construction process and tunnel maintenance once in operation.
Once an element is ready for deployment, it has waterproof bulkheads fitted at both ends before being towed into place using tugs. Then, with millimeter precision, the ‘elements’ are lowered into a 12-meter-deep trench dredged into the seabed before they become coupled.
The sealed space between the bulkheads is developed so that when water is pumped out, the external water pressure pushes them together. This ability makes a partial vacuum and guarantees a watertight connection.
Once all elements are assembled, technical and mechanical installations can begin. These comprise railway tracks, ventilation systems, cameras, communication systems, signage, and painting.
Although it is predicted that sea currents will ultimately cover the tunnel with sand, the last phase will see the tunnel covered with a protective layer of stone.