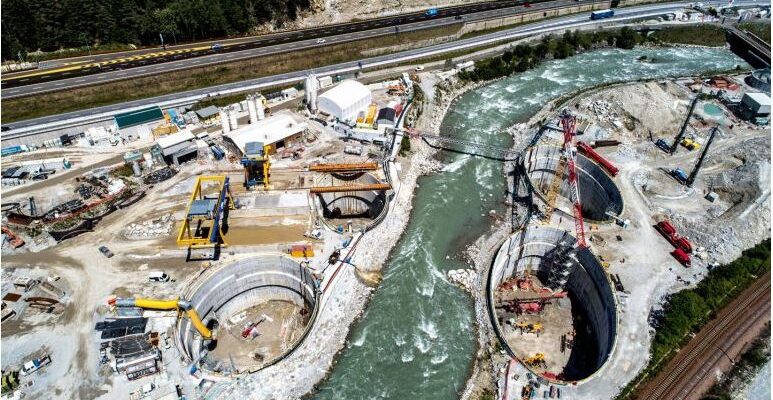
The 25 finalists for this year ITA Tunnelling Awards have been announced.
Judges selected the finalists from more than 100 entries received from 19 countries.
The winners will be announced at the ITA Awards Symposium on November 28 in Genoa, Italy. It is being held in conjunction with the two-day Italian tunnelling congress organised by the Italian Tunnelling Society (SIG).
The finalists are:
MAJOR PROJECT OF THE YEAR (€500m+)
Chunfeng Tunnel – Single-bore, double-deck Municipal Tunnel in Shenzhen, China
The Chunfeng Tunnel aims to reduce congestion and pollution in the city’s densely populated Futian and Luohu districts. Spanning 5.078km, with a 15.8m diameter, the double-deck tunnel supports a four-lane road and is constructed using slurry balance TBMs. It passes through complex geological formations and beneath numerous existing structures. The project incorporates innovations such as 78% prefabrication of tunnel structures and advanced cutterhead wear detection, saving €6m.
LIRR Grand Central Madison – New York City Terminal
Grand Central Madison is a landmark $11.1bn project by New York’s Metropolitan Transportation Authority (MTA), providing direct Long Island Rail Road (LIRR) access to Manhattan’s East Side. The underground terminal spans over 65,000m2, with eight new tracks and four platforms housed in two massive caverns. The project involved 9.7km of hard rock tunnelling under Manhattan and 3.2km of soft ground tunnelling in Queens, completed using techniques such as ground freezing. By transporting materials through tunnels to Queens, thousands of trucks were removed from the streets. Opened in 2023, it increases LIRR capacity by 40% and reduces daily commute times.
Thames Tideway Tunnel – London
The Thames Tideway Tunnel is an innovative solution to modernise London’s outdated Victorian sewer system. Spanning 25km, the tunnel intercepts 34 combined sewer overflows to prevent untreated sewage from flowing into the River Thames. Costing £4.5bn, the project employed six TBMs operating simultaneously in a dense urban environment. Extensive use of the Thames for transporting materials reduced environmental impacts such as carbon emissions and heavy vehicle traffic. Once operational, the tunnel will have a 120-year lifespan and reduce sewage discharges into the river by 95%. The project also featured technical innovations like using electric-powered drilling machines to lower noise pollution.
Thomson-East Coast Line Contracts T222 to T310 – Singapore
The Thomson-East Coast Line (TEL) is a fully automated mass rapid transit line in Singapore, covering 32 stations over approximately 43km. The section under contracts T222 to T310 spans 15km and includes 13 stations, constructed with the help of 18 earth pressure balance TBMs. With a total tunnel drive length of 29.4km, the €3.2bn project faced challenges like complex geology and interference with existing infrastructures. Ground freezing was used to minimise urban disruption.
PROJECT OF THE YEAR (€50-500m)
Lot H52 Hochstegen – Brenner Base Tunnel – Austria
The Brenner Base Tunnel (BBT) is a key infrastructure project connecting Fortezza, Italy, to Innsbruck, Austria. Lot H52, the Hochstegen section, involved the construction of 5km of tunnels, including an exploratory tunnel and main tunnel sections. Innovative solutions were required to manage complex water-bearing geological conditions, using specialised drilling and grouting techniques to stabilise the tunnel. This section of the BBT was completed in December 2023, contributing to a sustainable future by reducing road congestion and environmental impacts.
Lot H71 Isarco River Underpass – Brenner Base Tunnel – Italy
Lot H71 of the Brenner Base Tunnel project, focuses on the challenging Isarco River underpass, where tunnels were constructed with minimal overburden under major infrastructures like the A22 motorway and the Isarco River. Advanced techniques, including artificial ground freezing, were used to stabilise the ground and prevent river displacement. Spanning 6.2km, the project involved both single- and double-track tunnels. The innovative methods employed not only addressed the complex geological conditions but also ensured the project stayed on time and within budget.
Musaimeer Pump Station and Outfall Project (MPSO) – Qatar
The Musaimeer Pump Station and Outfall Project (MPSO) is a crucial infrastructure development in Doha, Qatar, aimed at managing groundwater and stormwater over an area of 270km2. The project includes a pump station, a 10.2km outfall tunnel (one of the longest in the world), and a seabed diffuser for treated water discharge. The tunnel was constructed using a TBM under challenging wet and dry conditions, with precise alignment achieved at a tolerance of 200mm. Despite the Covid-19 pandemic, the tunnel was completed 58 days ahead of schedule. The project has improved urban water management and helped protect over 30% of Doha’s population from flooding. All excavated materials were used for land reclamation.
SMP4 Lyon-Turin Saint-Martin-la-Porte Exploratory Tunnel – France
The SMP4 exploratory tunnel is part of the Lyon-Turin rail project, a vital element of the Trans-European Transport Network (TEN-T). The 12.7km tunnel serves both as a geotechnical investigation and a critical section of the future Mont-Cenis Base Tunnel. The project faced complex geological challenges, including unstable carboniferous formations, which were addressed using innovative methods such as bi-component grouting and controlled yielding support systems. The tunnel contributes to the shift from road to rail transport, reducing CO2 emissions and improving the capacity of freight and passenger trains across the Alps. It was completed in September 2022, marking a significant milestone for the broader Lyon-Turin project.
RENOVATION OF THE YEAR
Genoa Railway Junction Capacity Upgrade – Italy
The Genoa Railway Junction upgrade is a critical infrastructure project aimed at enhancing the city’s capacity to manage freight and passenger traffic. This renovation includes the construction of several new tunnels and the rehabilitation of abandoned ones, such as the San Tomaso, Polcevera, and Campasso tunnels. Innovations like widening the Facchini Tunnel for larger freight trains and reusing sections of the old Grazie Bassa Tunnel for emergency access improved project sustainability. The project is part of the broader effort to connect the Port of Genoa to the Trans-European Corridor, linking it with Rotterdam. The work ensures the separation of regional and long-haul trains, allowing for more efficient freight and commuter services.
Manfreida Tunnel Renovation Project – Italy
The Manfreida Tunnel renovation, part of the Genoa-Gravellona Toce motorway, adopts the Tunnel Renewal Strategy (TRS), aiming to extend the service life of the tunnel by 50 years. The project involved partially demolishing the existing lining and rebuilding it with innovative materials to improve waterproofing and structural integrity. The renovation is divided into two phases to minimise traffic disruption, using technologies like prefabricated elements and high-performance sprayed concrete. By using a multi-criteria analysis for optimal solutions, the project focuses on safety, minimising impacts on traffic, and ensuring the long-term resilience of the infrastructure.
Refurbishment of the Heinenoord Tunnel – Netherlands
The Heinenoord Tunnel, constructed in 1969 using the immersed tube method, serves over 110,000 vehicles daily. The renovation project involves the complete replacement of tunnel technical installations, concrete repairs, and asbestos removal. A significant challenge was the addition of a central gallery for safer escape routes, which was built using prefabricated elements over four weeks in the summer of 2023. By pretesting and using mock-ups, the work was streamlined to minimise traffic disruption. Despite closures for necessary works, the project aims to reduce future interruptions, improve tunnel safety, and ensure faster completion. It is set for completion by December 2024, with a total cost of approximately €200m.
TECHNICAL INNOVATION OF THE YEAR
Advanced Tunnelling Assistance System – Italy
The innovative Advanced Tunnelling Assistance System (ATAS) implements real-time TBM data analysis and monitors data using AI/machine learning. This permits continuous monitoring of the excavation and perform, from the measured parameters, estimates on the variation of geological conditions at the excavation face. In addition, ATAS constantly updates settlement criteria evaluations based on real-time added information and permits automatic evaluation of new excavation parameters (such as adjusting face pressure) to mitigate the risk. The system has been applied for the first time on one of four 8.78m diameter TBM drives excavated for a rail node development project in the centre of Łódź in Poland. The ATAS takes advantage of existing data to optimise TBM excavation and reduce excavation risks. This is particularly important in urban areas, where the consequences of accidents can be extremely severe.
Disc cutter wear sensor package and TBM monitoring system – South Korea
Newly-developed technology that maximises excavation efficiency by remotely measuring disc cutter wear using a package comprising magnetic sensors, hall sensors, a power supply battery, a wireless communication module, an Arduino board, and an external casing. As the disc cutter ring wears, the relative distance between the ring and the magnetic sensor increases. This affects the magnetic flux density which can be detected by the sensor, thereby obtaining voltage measurements. Using these voltage values from the sensor, the relative distance of the disc cutter ring can be calculated. A deep learning-based algorithm for assessing wear conditions and predicting the remaining cutter life has been developed, which can be provided to users through the monitoring system. The innovation lies in measuring the wear of disc cutters through sensors instead of relying on man-entry interventions, allowing for data-based decisions on when to replace the disc cutter.
MIRET-Tunnel AI – Italy
MIRET, Management and Identification of the Risk for Existing Tunnels, is a methodology, an IT environment and a series of tools for planning and management of infrastructures and tunnels, aiming at the digital transformation of the whole asset management and life cycle, from element inspection to decision-making. MIRET combines mobile mapping surveys, AI for analysis, digital models, risk analysis and shared working environments. Inspections are performed using ARCHITA, an ETS system for the multi-dimensional mobile mapping of tunnels that integrates laser scanners, ground penetrating radars, and linear and thermal cameras on a bimodal vehicle with a survey speed of 15-30km/hr. ARCHITA moves the inspection phase from on-field to back-office guaranteeing more reliable and cost-time efficient data. The digitalisation is performed from 3D point cloud to CAD and IFC, with a good level of information from the integration of HD photos, radargrams and thermal images. Currently, the data refers to the years from 2017 to 2023. These data are subject to a quality control process, where the preparation of the vulnerability map is carried out by a specialist engineer and/or geologist.
PRODUCT/EQUIPMENT INNOVATION OF THE YEAR
Advanced Hybrid Wireless Sensor Network System for safety risk sensing in tunnel and underground engineering – China
Real-time wireless sensor monitoring systems have been heavily applied in daily monitoring projects globally. Existing systems, however, reach a limit when three critical monitoring challenges are encountered: unstable data transmissions in an underground construction environment; non- cooperated measurements when using mixed systems from various suppliers; and slow response to early warnings when wireless sensors are in deep battery saving hibernation mode. The Advanced Hybrid Wireless Sensor Network (H-WSN) System addresses these challenges. It has original, systematically embedded software designed on wireless communication protocol of Static Mesh for long-term trend, Trigger Mesh for trigger event detection, and Dynamic Mesh for high volume data handling; complete, original, systematically embedded hardware design to interface all the major categories of sensors; and high quality, reliable, instant data for safety risk sensing, management and control. Since March 2021, the H-WSN has served 1,200 commercial projects in 20 countries and is credited with avoiding 300 major accidents by timely warnings in the real world. Extensive collaboration with international university researchers and industrial colleagues, has generated significant economic, social, and environmental benefits for tunnel and underground engineering community.
Deep Underground Type 0-90° Continuous Conveyor Equipment – China
The 0-90° continuous conveying equipment continuously transports TBM excavated material along tunnels and up inclined or vertical shafts to the surface. The horizontal system uses a common flat belt to convey soil to the bottom of the inclined or vertical shaft while the 0-90° lifting system is usually a corrugated edge conveyor belt that changes direction through various rollers, forming a closed circular structure with continuous rotation. The continuous conveyor equipment effectively solves the problem of rapid vertical transportation of excavated material from shield tunnel headings to improve the efficiency and safety of muck handling and discharge. The operating speed can be adjusted automatically based on the amount of excavated material produced and the control system is equipped with functions such as leakage protection, overload protection, and no-load protection to ensure the safe operation of the vertical lifting system. Compared with traditional spoil removal methods, it increases excavation efficiency by 33% and reduces energy consumption by about 30%.
SOGUN: Geometric Control System for Shotcreting and Other Tunnelling Works – Spain
Developed by Dragados, SOGUN advances tunnel construction technology, particularly in shotcrete applications. In an automated process, SOGUN scans the tunnel in 3D with an integrated LiDAR to generate a surface point cloud. This data is compared to the pre-loaded theoretical surface and an image is projected on the tunnel wall, indicating areas of excess or missing concrete thickness. This process is completed in under a minute. The shotcrete operator then needs only to look at the tunnel to understand the task to be performed as displayed in areas of different colours according to numerical information about the difference between the actual and the theoretical tunnel surfaces. Additional applications include determining over- or under- excavation and checking the tunnel’s dynamic gauge to detect clashing areas with the tunnel surface. SOGUN enhances productivity, reduces costs, and minimises workers’ risks, introduces superior quality finishes, and improves sustainability by optimising material usage and reducing waste.
Ultra-small turning radius hard rock TBM – China
The horizontal turning radius of a conventional TBM is about 300-500m. However, the 4km route of the 3.53m diameter drainage corridors from the first layer to the fourth layer for the Jinyun PumpedStorage Power Station in Zhejiang Province, required a TBM with a turning radius of less than 30m, about 10 times the tunnel diameter. A TBM was designed and developed by CREG, China Railway Engineering Equipment Group, and was launched in November 2021. After boring 22 sections with a turning radius of 30m, it achieved maximum monthly advance rates of 660.5m and a maximum daily advance rate of 38.38m. In December 2022, the TBM successfully broke through, six months ahead of schedule.
BEYOND ENGINEERING
City Rail Link – New Zealand
Auckland’s City Rail Link comprises 3.45km of twin tunnels connecting four train stations. It will double rail capacity and create new public spaces. Working beyond engineering, City Rail Link referenced local history and prioritised a strong partnership with the indigenous Māori mana whenua tribes, working together on design, environment and social outcomes. Two new underground stations are named Karanga-a-Hape and Te Waihorotiu, and two existing stations with Māori names Maungawhau and Waitematā are redesigned to accommodate new nine-car electric trains. The EPBM that excavated twin 1.6km bored tunnels was named in recognition of the Māori rights activist Dame Whina Cooper.
Eco-friendly metro construction for challenging coastal geological environments – China
The Qingdao Metro Line 6 (Phase I) Project is a demonstration project approved by the National Development and Reform Commission. It spans 30.8km with 21 underground stations and about 25km of connecting running tunnels. The project has developed and promoted prefabrication and assembly construction technologies for urban mass transit, making it the metro line with the largest application scale of such technologies in China. The stations employ a simple decoration process using fair-faced concrete, and the decoration design in public areas effectively combines functionality with artistry. This has advanced the eco-friendly and low-carbon transformation and upgrading of Qingdao Metro construction. All production and installation processes have been localised, stimulating an industrial scale worth RMB1.3bn.
Modern underground cemetery – Israel
Enabling the reuse of the space beneath an existing cemetery, the underground cemetery is a first-of-its-kind, designed, excavated, and constructed in compliance with the requirements of an ultra-Orthodox community. Using state-of-the-art design and construction methods while working within the constraints of the existing urban zoning and regulations, the underground cemetery revives Jewish burial traditions that were prevalent more than 2,000 years ago. Planning and construction of the project solves an acute shortage in burial space while avoiding encroachment on sensitive open space.
Risk control for safe shield tunnelling through complex strata of the Pearl River System – China
The 4.76km section of the Guangzhou Metro Line 18 between Shaxi and Shiliugang Stations in Panyu District runs through highly weathered muddy formations with the groundwater influenced directly by the Pearl River tidal action creating frequent water head fluctuations. Significant risk management and control technology was developed to support the shield TBM drives of the twin tunnels as they passed under three rivers, beneath three viaducts and more than 20 buildings, and alongside the South China Expressway Viaduct. The project has established stable risk prevention measures and systems which have controlled the shield tunnel drives.
YOUNG TUNNELLER OF THE YEAR
Adriano Martoccia – Italy
Since completing his studies as a structural and geotechnical civil engineer seven years ago, Adriano Martoccia has worked in the technical department of contractor Ghella. To date he has worked on several diverse projects in Italy and abroad and is currently a senior project engineer on the Trento high-speed railway project leading a team setting up for launch of four dual mode TBMs to excavate 20km of twin tunnels.
Hanan Samadi – Iran
After graduating from University of Tehran with an MSc in engineering geology, Hanan Samadi, is advancing her career in a male-dominated industry and in a fiercely traditional country. Through her pioneering work in machine learning and AI in Iran, Hanan has made tangible differences in the environment in which tunnelling machines operate.
Luigi D’Angelo – Italy
Currently working as a project engineer for Italferr on the Naples-Bari high speed railway, Luigi D’Angelo is proposing a gradual move to a new role providing support and co-ordination to underground projects all over Italy with the aim of helping to standardise design choices and processes to improve and simplify the productive chain for clients and all parties involved.