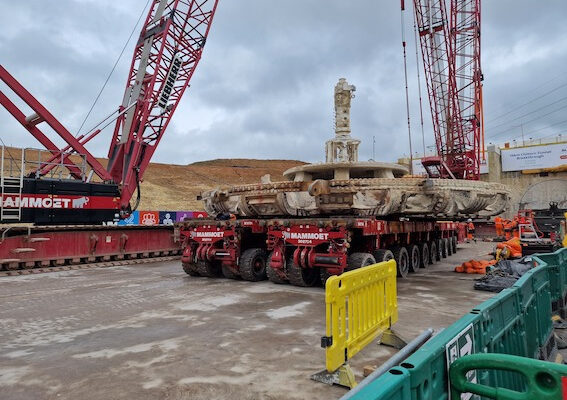
The process of dismantling TBM Florence and TBM Cecilia which broke through on HS2’s longest tunnel respectively on February 27, and March 21 has been completed. The two Herrenknecht machines were 170m long and weighed 2,000 tonnes.
The responsibility of dismantling these TBMs at the north portal after they each completed their 16.1km journey was up to Mammoet, which supported Align JV with the assembly of the two TBMs at the south portal.
According to Mammoet senior commercial manager Simon Crawley: “The restrictions at the north portal meant the equipment used to build the TBMs wasn’t necessarily what was needed for their dismantling. There were different limitations at the two sites. Because there were obstructions in the way, a 600t crawler crane was needed at the construction stage. We believed that a 400t crawler crane would be adequate to perform the dismantling.”
In order to creating a visualisation of the project using Move3D, to prove a lower capacity crane could do the job, Crawley worked with Mammoet project manager Rhys Burley, and project engineer Antreas Michail, which included a full animation of the most complex lifts.
The 400t capacity crawler crane was used to remove the biggest components from the TBMs. To remove the cutterhead, an LR1300SX crawler crane was also used to perform a tandem lift.
Considering that the components were lowered onto Mammoet self-propelled modular transporters (SPMTs) before being taken to one of two laydown areas, additional crawler cranes, including the LR1300SX and an LR1250 support crane, offloaded the components onto the ground or supports for further dismantling.
Additionally, due to that the cutter head was too heavy for the smaller cranes to lift, climbing jacks were used to offload it from SPMTs to the ground.
While the cutterhead’s center of gravity could not be fully known, this was another challenge and the lifts also required to be performed on a slight incline because the TBMs exited the tunnel at an angle. Typically, challenges such as this would require additional drawings and management of changes before performing the lift, which would add delay. Mammoet, however, developed an engineering solution.
“We used air hoists to make pneumatic length changes and keep the components level, It took away that manual element of hoisting chain blocks. It was done on a compressor rather than using manual labour, which was safer and more efficient,” said Burley.
Also Crawley added: “The key challenge was the large amount of equipment and number of people needed for the project.”