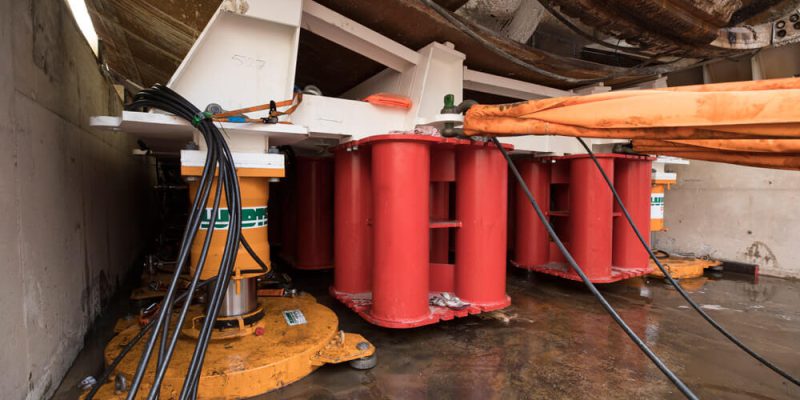
In order to rotating the first section to the TBM in the reception chamber, engineers working on London’s Silvertown Tunnel have used nitrogen skates.
As the largest TBM to be used in the UK, this Herrenknecht machine has a 11.91m diameter and its first section was successfully turned 180 degrees in just one day by engineers during the previous weekend using an air cushion system developed by Herrenknecht and its partners.
Following completion of the 1.1km southbound drive from Newham on February 15, TBM Jill reached the 40m rotation chamber in Greenwich. The 82m-long TBM is now being rotated in sections before being reconfigured and reassembled to dig the second bore under the Thames to Newham.
According to Herrenknecht’s announce on LinkedIn: “This impressive achievement would not have been possible without the teamwork of our 10 Herrenknecht service experts and the crew members of the Riverlinx JV. They worked hand-in-hand to ensure the machine was turned smoothly in the shaft after completing its first drive.”
With an average daily performance of 18m, the TBM was commissioned from Newham in September last year.
Linking Newham on the north of the Thames to the Greenwich Peninsula on the south side, the twin-bore Silvertown Tunnel is due to be opened in 2025 and it is going to ease congestion at the Blackwall Tunnel.
The Riverlinx CJV, that is a joint venture comprising BAM Nuttall, Ferrovial Construction and SK ecoplant, is responsible for delivery of this project.
A time lapse video of the TBM rotation has also been attached below.