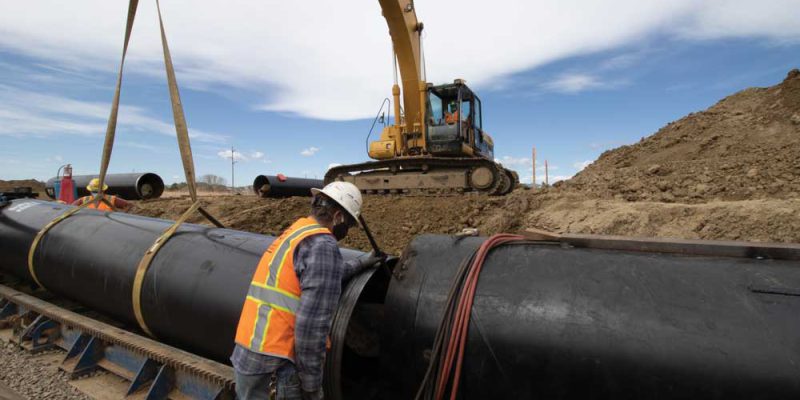
Having completed a recent auger boring project in Berthoud, Colorado, the team from BTrenchless was presented with a unique opportunity. The project involved two identical bores under US 287, a major six-lane highway in Berthoud, about 50 miles north of Denver, which all allow BTrenchless to compare the efficiency of new spiral-welded steel jacking pipe with a push-together joint from Tri-Loc vs. standard, tried-and-true welded steel pipe.
The project bores were exactly the same diameter (42 in and length (200 ft), located less than 10 ft apart side-by-side, going across the same ground conditions and with the same amount of protection. Thus, BTrenchless, a BT Construction division located in Henderson, Colorado, agreed to take advantage of the scenario to use the numerous pipe materials to fix each bore.
BTrenchless Project Manager, Matt Wojtkiewicz pointed out, “The main thing we wanted to see was if the Tri-Loc pipe with locking joint could be used efficiently vs. welding the pipe,” He also added, “Specifically, does the cost of the Tri-Loc pipe offset the welding cost of standard pipe? Since we had two tunnels of the exact same length within 10 ft of each other, it was a perfect place to test it.”
This the initiative for the Department of Transportation of Colorado included twin auger bores under US 287 to provide stormwater drainage infrastructure for the development of a new housing subdivision. The project was finished in April and May 2020, and the project went off without a hitch except one snowstorm that affected the city.
Boring developments
To complete both bores across the land that included fill and claystone bedrock and Pierre shale, crews used a McLaughlin auger boring machine with an On-Target steering system. Afterwards, using 20-ft steel pipe segments with welded joints, the first bore was completed. After this successful completion of that bore, crews repositioned the machinery in the pit and continued using Trinity Products’ Tri-Loc spirally welded tubing for the second bore.
The pipe is made by Trinity Goods at its St. Charles, Missouri, plant. More importantly, a machined joint mounting system is integrated into the pipe that reduces the need for field-applied butt welds. Under tremendous ground strain, the joints turn to flat on the inside and outside as well as leak-proof. 24 to 120 in. are required for the pipes. OD with a thickness of the wall ranging from 0.375 to 1.5 in.
In a range of trenchless construction applications, including microtunneling, pipe jacking, auger boring and pipe ramming, tri-Loc pipes would be finally ready to be used.
As stated before, in conjunction with the press fit attachment joints, BTrenchless was hoping to quantify the cost-effectiveness of the spiral welded pipe, but it was also eager to see the efficiency of the spiral-welded pipe itself. When it was advanced into the ground, a spiral-welded pipe from the past had built a twisted reputation, a concern that Trinity solved by reducing the protrusions of the weld seams on the outside of the pipe.
Don Meyer, BTrenchless Superintendent asserted, “The old school of thought was that spiral-welded pipe would start twisting as it goes through the ground, almost like a screw, because of the welds on the outside of the pipe,” he also said, “We had a little bit of rotation when installing the pipe, but it was nothing out of the ordinary. The Tri-Loc pipe still has seams on the outside of the pipe, but they are not like the big welds that you would see 25 years ago.”
Boosting Efficiency
The advantages of using press fit joints, such as Tri-Loc vs. full butt welds, became obvious as the project proceeded. Using welded tubing, teams averaged 40 ft a day and were able to double output using the Tri-Loc pipe.
The main explanation for the efficiency improvement is the time it takes to finish the process of welding vs. lowering in a new pipe segment and progressing it until the joints click together. On average, it will take about 2 hours for crews to prepare and weld the traditional pipe parts, versus 23 minutes for the Tri-Loc pipe to be packed.
Chris Knott, lead Trenchless Estimator for BTrenchless also said, “As production goes up, it is a cost savings to us,” He also added, “Having a crew waiting for 23 minutes vs. 2 hours makes a big difference.”
Furthermore, Tony Baker, Sales/Project Manager for Trinity Products said, “We’re trying to make it easier on our customers by making a pipe that eliminates welding and reduces time in the field, allowing them to get the job done quicker and move on to the next one,”
Wojtkiewicz also put it this way, “Overall, it was a good project and the pipe itself was great,” He claims that in choosing between the standard welded pipes and pipes like Tri-Loc, the larger the diameter and the longer the run, the more sense it makes to go with a pipe like Tri-Loc.” He furthermore stated, “Going in, we had a concern about the pipe rotating and getting off line due to the spiral weld, but that wasn’t an issue in our case, especially since we were in sandy gravel and not in clay. Importantly, we were able to minimize downtime and keep our crews productive all day.”