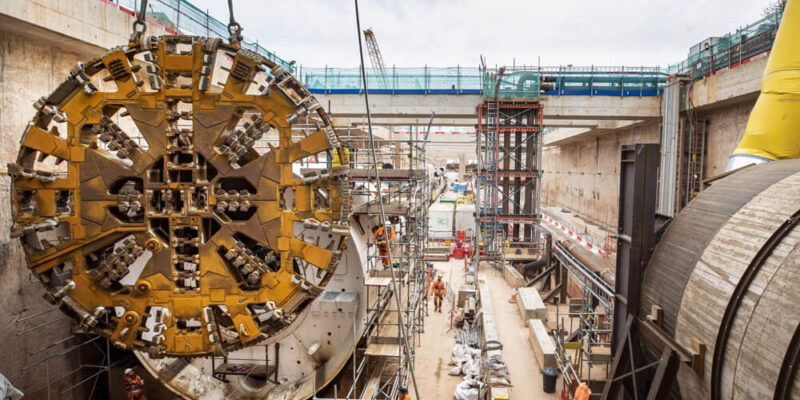
In order to commencing the digging process of second bore of the 3.5 mile Bromford Tunnel into Birmingham in coming year, a team of 90 specialist engineers have completed the assembly of HS2’s giant tunnel boring machine (TBM).
Using two 600 ton cranes, sections of the machine such as the huge 125 ton cutterhead were moved into a 12-metre deep launch pit at the front of the 125-meter-long machine in the pit bottom.
Mary Ann that was the first TMB and named after Mary Ann Evans (the real name of Victorian writer George Eliot who was born in Nuneaton), started tunneling the first bore from the east portal site near Water Orton in August this year. It has already built more than 500 tunnel rings, which is 0.6 miles of the 3.5-mile-long tunnel between North Warwickshire and Washwood Heath in Birmingham.
The determined date for publishing the name of second TBM is due to be before it launches in Spring next year. While the scheduled date for breakthrough of Mary Ann is set to be the end of 2024, the second TBM planned to complete its journey in the middle of 2025.
The amount of excavated material by these TBMs will be 1.87 million tons and are slated to be sifted at the on-site slurry treatment plant and reused on HS2’s nearby sites at Delta Junction, where a complex network of nine viaducts is being built.
HS2’s Senior Project Manager Catherine Loveridge said: “With the first TBM ‘Mary Ann’ well on her way building the tunnel to take high speed trains into central Birmingham’s Curzon Street Station, it’s fantastic to see the second TBM assembled and being prepared to start digging. We’re now at peak construction, with over 9,750 people working on HS2 in the West Midlands and around 450 people working on this site, including many from the local area. Launching the second TBM next year means there will be more exciting jobs up for grabs for local people.”
Following completion of the one-mile twin bore Long Itchington Wood Tunnel in Warwickshire earlier this year, the gantries and the center part of the cutterhead of TBM Dorothy have been re-used for construction of the second TBM.
Disassembled sections of Dorothy’have been moved to the Bromford Tunnel portal site near Water Orton over the last few months, where they have been lowered and reassembled into the underground launch area.
Considering that the trains will be travelling slower on the approach into Birmingham Curzon Street Station, at 8.62 meters in diameter, the Bromford Tunnel is smaller than the 10-meter diameter Long Itchington Wood Tunnel, so the TBM required a new outer part cutterhead and a new shield, which were manufactured by Herrenknecht in Germany.
While the number of persons who deliver full Bromford Tunnel program is around 450 people working for HS2’s contractor Balfour Beatty VINCI (BBV), in order to operating the TBM 24/7 with each bore of around 16 months, a specialist tunneling team, including apprentices working for BBV’s sub-contractor Tunnelcraft.
According to Jules Arlaud, Tunnelling Director for Balfour Beatty VINCI:
“Completing the assembly of the second tunnel boring machine is another major achievement for the team working on HS2’s Bromford Tunnel – a complex section of the new high-speed railway. Getting to this stage has required a huge amount of planning and preparation, including the disassembly and transportation of ‘Dorothy’ parts from Warwickshire, which forms the majority of the second TBM.”
He continued: “Over the next few months, the team will be busy testing, checking and carrying out the final preparations, to make sure the machine is ready to start digging in spring next year.”
The Bromford Tunnel program includes designers from Balfour Beatty VINCI’s Design Joint Venture, made up of Mott MacDonald and SYSTRA (MMSDJV).
Rosa Diez, Tunnels Discipline Lead for MMSDJV said: “Seeing the second TBM in position, ready to start, is a proud moment for our tunneling team. We have learnt so much from the excavation of the Long Itchington Tunnel by our ‘Dorothy’ TBM, which has helped get Mary Ann well on her way through the Mercia Mudstone in the Bromford Tunnel. The learning will continue for this second TBM, which once named and launched next year, will also become part of our family.”
For completing the twin bore tunnel, a total of 41,594 concrete segments will create 5,942 rings with each ring weighing 49 tons.
The location of manufacturing these segments is at Balfour Beatty VINCI’s pre-cast factory at Avonmouth near Bristol and in the concrete mix used at the factory 40% of the cement is replaced with Ground Granulated Blast-furnace Slag (GGBS) which has a much lower carbon footprint than traditional cement. 3D scanning is used in the production process of the segments to guarantee accuracy.