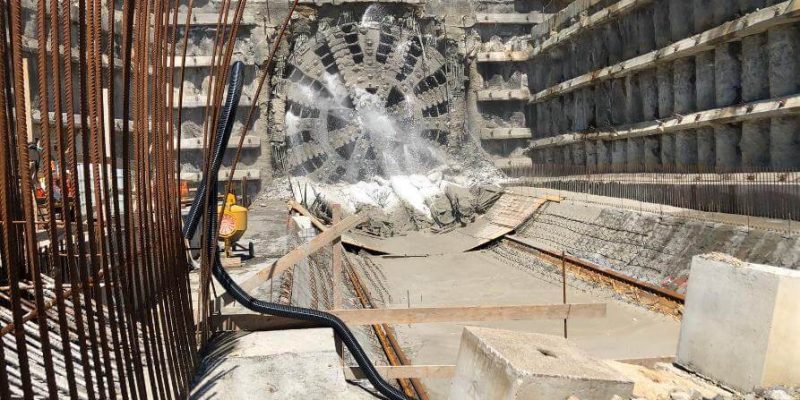
Locating in the new three-lane Barberino di Mugello – Florence North section of the A1 motorway in Barberino di Mugello, Italy, MAPEI‘s UTT Division has presented technological solutions and technical assistance for all the main applications related to excavation of the S. Lucia tunnel.
Two emphasized aspects of constructing this tunnel by MAPEI are:
- The dimensions: considered as the largest machine ever used in Italy and one of the largest ever in the world, the TBM EPB with a diameter of 15.90 m was used for boring this tunnel.
- MAPEI aims to highlight the issue of the environmental effect of the tunnel. This tunnel project was among the first in both Italy and the world, in which particular attention was paid to minimizing the environmental impact of the products used for soil conditioning during the excavation.
Significant helps of MAPEI UTT’s technical was in the following steps:
Tunnel segments casting
MAPEI provided products for the mix design of precast concrete used to make the tunnel segments – dimensions (55 cm thick and 2.2 m long) were particularly high precisely because of the excavation diameter of the tunnel itself. Dynamon NRG1015SC and Dynamon NRG1037, super fluidifying additives were specifically formulated for this application, and Mapeform W60, a universal formwork release agent, was also used.
Ground Conditioning
During the excavation of about 8 km of tunnel, Polyfoamer ECO/100, a foaming agent based on surfactants in combination with a natural polymer, was used to condition the soil at the shield. Polyfoamer ECO/100 differs from traditional foaming agents in that it has a very low environmental impact on water and excavated soil.
This product was selected for the S. Lucia tunnel because it was the best in terms of technical and environmental performance, among all those that were tested in the preliminary phases. Testing was carried out by both the Turin Polytechnic laboratory (which carried out the technical conditioning tests) and by the Rome laboratory of the CNR (which carried out the environmental biodegradability and eco-toxicity tests).
The use of Polyfoamer ECO/100 throughout the tunnel allowed the company both to advance the excavation quickly and safely and to minimize the environmental impact on the soil and consequently reduce the time required to store it on-site before transporting it to its destination. About 1.5 million cubic meters of soil were excavated and conditioned with Polyfoamer ECO/100.
Backfill injection mix
The annular void between the segments and the soil was filled with a two-component cementitious mix, specially developed in the MAPEI laboratory using Mapequick CBS System 1L, a retarder additive with fluidifying effect, and Mapequick CBS System 3, an accelerator.
Restoration of the concrete in the segments
The defects in the concrete of the segments were repaired using MAPEI cementitious mortars and leveling compounds from the Mapefer, Mapegrout, and Planitop ranges. In addition, Resfoam 1KM Flex single-component polyurethane resin was used for secondary injection on the back of the segments in the event of water infiltration.